Square Threads
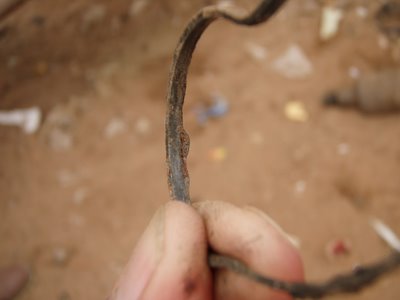
I know that anyone who has ever tightened a nut and bolt has probably seen stripped threads…
I know as well that broadly square section threads (I’m including Acme type threads in with this) have their place in drive systems such as lead screws. However square section threads have a major disadvantage where repeated shock loads, load reversals or load and unload cycles occur.
This is due to the sharp angle at the root of the threads.
The other morning, a piece of drilling equipment (the trip monkey for standard penetration testing) fell to pieces. A shaft, presumably of something akin to 0.4% carbon steel had pulled out of a presumably mild steel anvil.
On inspection, the threads from the anvil were still in place in the groove of the threads on the shaft.
Once these were peeled off, it became clear that the fracture had propagated from the sharp angle at the root of the thread and in some places, had actually passed below the root on the opposite side of the thread.
What importance has this?
Well, around the end of the 19th and beginning of the 20th century, intuitive craftsmen knew that cracks started from sharp angles in stressed objects. However it seems that some (perhaps almost all) university trained engineers assumed that the stresses were carried uniformly through the solid, hence we see rifle actions such as the 1903 Springfield and the 1914 and 1917 Enfield with square form threads in the receiver rings.
It was only much later that Griffith undertook his research on stress concentrations and crack propagation.
Highly stressed threads, such as those in rock drills are now of “rope” form, with no sharp angles to form stress concentrations.
The Springfield and Enfield have proved their reliability with many having shot out several barrels in their long lifetimes, this is despite, not because of the square form barrel threads.
0 Comments:
Post a Comment
<< Home